Plastic extrusion for tubing, profiles, and custom shapes
Comprehending the Basics and Applications of Plastic Extrusion in Modern Production
In the world of modern production, the method of plastic extrusion plays an important duty. Unwinding the principles of this procedure exposes the real flexibility and possibility of plastic extrusion.
The Principles of Plastic Extrusion Refine
While it may appear complex, the fundamentals of the plastic extrusion process are based on reasonably simple concepts. It is a manufacturing procedure in which plastic is thawed and after that shaped into a continual account with a die. The raw plastic material, typically in the kind of pellets, is fed right into an extruder. Inside the extruder, the plastic goes through warmth and stress, causing it to thaw. The liquified plastic is after that required via a shaped opening, known as a die, to develop a long, constant item. The extruded product is cooled and afterwards cut to the wanted size. The plastic extrusion process is thoroughly used in numerous sectors due to its performance, versatility, and cost-effectiveness.
Various Sorts Of Plastic Extrusion Methods
Building upon the fundamental understanding of the plastic extrusion process, it is needed to discover the different strategies associated with this manufacturing approach. The 2 key strategies are profile extrusion and sheet extrusion. In profile extrusion, plastic is melted and developed right into a constant profile, often made use of to produce pipes, rods, rails, and home window frameworks. In contrast, sheet extrusion creates large, level sheets of plastic, which are usually additional refined into items such as food packaging, shower drapes, and automobile components. Each strategy requires specialized machinery and exact control over temperature level and stress to ensure the plastic preserves its shape during cooling. Comprehending these strategies is essential to making use of plastic extrusion properly in modern manufacturing.
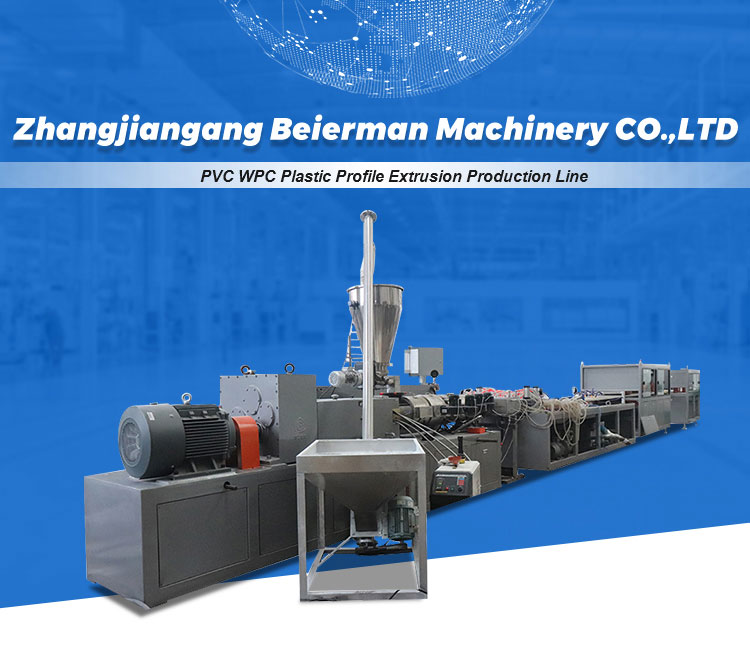
The Duty of Plastic Extrusion in the Automotive Industry
A frustrating bulk of parts in modern-day automobiles are products of the plastic extrusion process. Plastic extrusion is largely made use of in the manufacturing of numerous automobile elements such as bumpers, grills, door panels, and control panel trim. Thus, plastic extrusion plays an essential function in automobile here are the findings manufacturing.
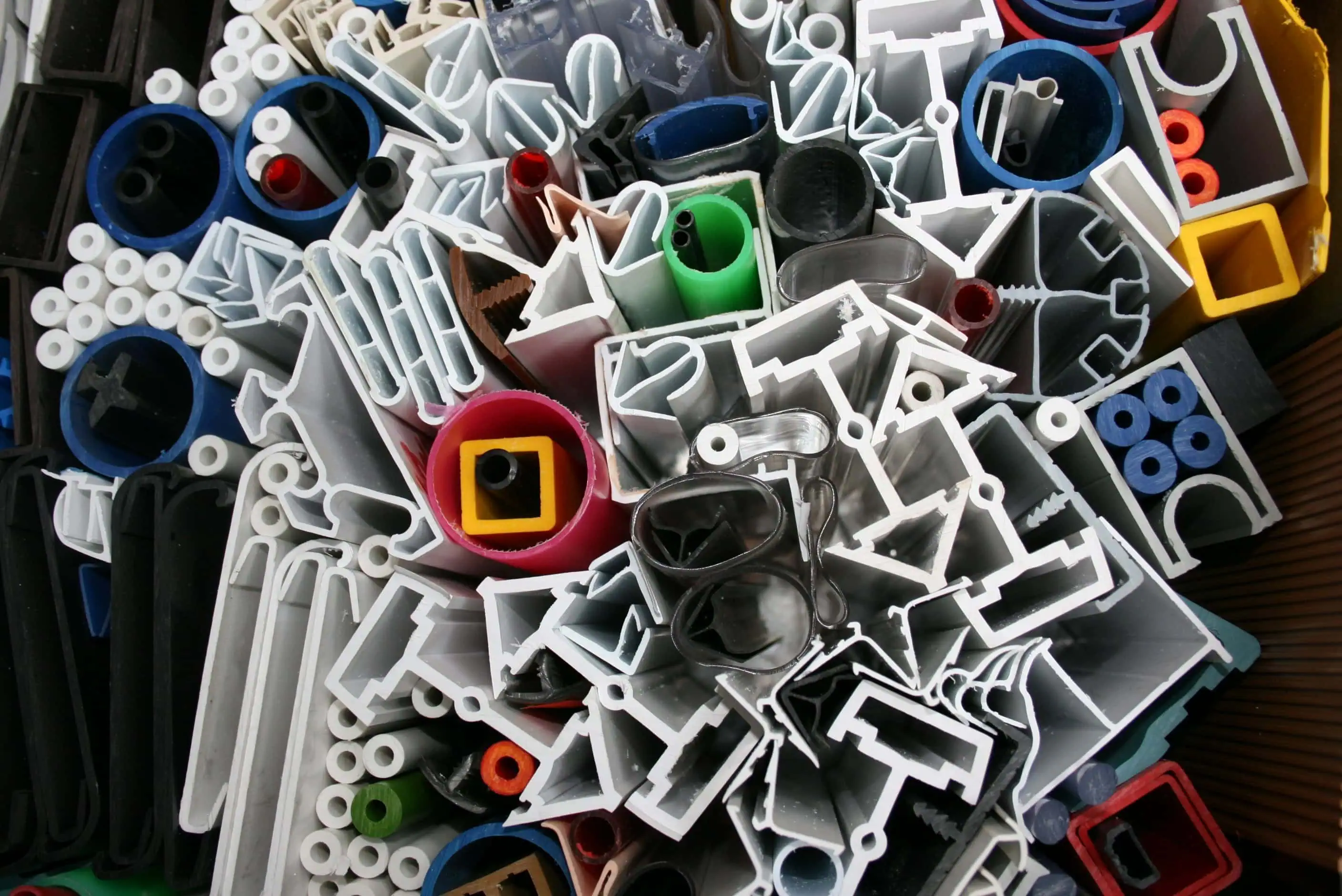
Applications of Plastic Extrusion in Durable Goods Manufacturing
Past its significant effect on the automotive market, plastic extrusion shows equally efficient in the realm of customer items making. This process is critical in producing a large range of products, from food packaging to home devices, playthings, and also clinical gadgets. The flexibility of plastic extrusion enables makers to create and create complicated forms and dimensions with high accuracy and efficiency. Due to the recyclability of numerous plastics, squeezed out components can be reprocessed, decreasing waste and cost (plastic extrusion). The flexibility, adaptability, and cost-effectiveness of plastic extrusion make it a favored selection for numerous consumer goods manufacturers, adding substantially to the market's development and technology. Nonetheless, the environmental ramifications of this prevalent use need cautious consideration, a subject to be reviewed additionally next in the succeeding area.
Ecological Impact and Sustainability in Plastic Extrusion
The prevalent use of plastic extrusion in making invites analysis of its eco-friendly implications. Efficient equipment decreases power usage, while waste management systems recycle scrap plastic, reducing raw product needs. Regardless of these renovations, even more development is needed to alleviate the environmental footprint of plastic extrusion.
Final thought
To conclude, plastic extrusion plays a vital role in modern-day manufacturing, specifically in the automobile and durable goods industries. Its versatility allows for the production of a vast array of parts with high precision. Additionally, its capacity for recycling and growth of naturally degradable products uses a promising method in the direction of lasting methods, thus addressing ecological worries. Comprehending the fundamentals of this procedure is key to enhancing its applications and advantages.

The plastic extrusion process is thoroughly made use of in different industries due to its performance, versatility, and cost-effectiveness.
Building upon the basic understanding of the plastic extrusion process, it is necessary to explore the different techniques entailed in this more tips here production approach. plastic extrusion. In contrast, sheet extrusion creates big, level sheets of plastic, which are normally more processed right into items such as food product packaging, shower drapes, and cars and truck parts.A frustrating majority of parts in contemporary lorries are products of the plastic extrusion procedure